1.影响疲劳老化的因素
橡胶的疲劳老化其实是由机械力、氧气、臭氧等多种因素综合作用产生的,其实质是一种力化学过程。橡胶自身的微观结构、使用时的环境、使用时的受力状况均对橡胶的耐疲劳老化性能有影响。采用德墨西亚屈挠试验机的实验表明,各种橡胶试样,抵抗产生裂口的能力为:丁基橡胶>氯丁橡胶>丁苯橡胶>丁腈橡胶>天然橡胶;而抵抗裂口增长的能力如表3-8所示。
图3-8 各种橡胶耐疲劳性能的比较
由表3-8可见,橡胶的耐疲劳性能为:丁基橡胶>天然橡胶>氯丁橡胶>丁腈橡胶>丁苯橡胶实验表明,丁苯硫化胶抵抗产生裂口的能力比天然橡胶硫化胶大四倍,但抵抗裂口增长速度却只有天然橡胶的三百分之。疲劳变形率(%)对各种橡胶的耐疲劳性能有不同的影响。在低变形率下,丁苯硫化胺和顺丁硫化胶都有良好的耐疲劳性能;而在高变形率下,天然硫化胺和异戊硫化胶却表现出良好的耐疲劳性能。这可解释为天然橡胶和异戊橡胶在高变形率下的结晶结构有助于提高耐疲劳作用。在硫化橡胶中,交联密度和交联键的类型对疲劳老化有很大影响。当交联密度过高时,由于橡胶分子链段的活动性下降,不利于分散应力,而使耐疲劳性下降。另外,在多次变形下,多硫键硫化胶比单硫键、碳-碳键硫化胶的工作能力强(疲劳寿命长)。图3-21可看出,在多次变形下,硫黄硫化胶(多硫交联)比秋兰姆硫化胶(低硫交联)的防老剂消耗速度慢,即说明多硫键硫化胶要比低硫键硫化胶的疲劳寿命长。因为多硫键的键能低,活动性强,在机械应力下可产生键的重排作用,因而易于硫化胶中应力的重新分配并均匀化,自然降低了机械活化效果,从而提高了工作能力和耐疲劳破坏性能 。
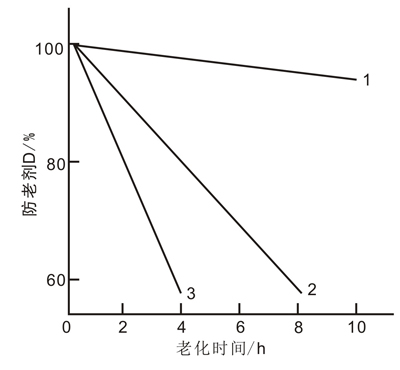
图3-21 不同硫化体系硫化胶疲劳老化时防老剂的消耗速度
1—秋兰姆硫化胶(无应力状态) 2—硫磺硫化胶(多次变形) 3—秋兰姆硫化胶(多次变形)
此外,填料的性质与橡胶的疲劳老化也有很大关系。活性填料(如炭黑)有较大的比表面积和较强的表面活性能使橡胶分子在其粒子表面形成一层致密的结构,使体系中橡胶分子空间分布的均匀性差异很大,在疲劳过程中这种不均质的状态容易产生应力集中现象,从而加速了疲劳老化过程;相反,活性小的填料,对橡胶分子的吸附能力小,在粒子表面上不能形成致密的结构,因而橡胶分子的空间分布较为均匀,在疲劳过程中橡胶分子受较小的束缚而具有较大的活动性,并易从填料粒子表面上脱落下来,减轻体系的不均质程度,结果出现了较好的耐疲劳老化性。
2.疲劳老化的防护
橡胶疲劳老化的有效防护方法是在胶料中加入屈挠龟裂抑制剂,它的作用是提高橡胶疲劳过程中结构变化的稳定性,特别是在高温条件下能发挥阻碍应力活化产生的氧化反应和臭氧化反应,一般有效的屈挠龟裂抑制剂多是一些酮和芳胺的缩合物(如防老剂AW、防些防臭氧老化和防热氧老化的防老剂BLE等)以及对苯二胺类防老剂。实践发现如防老剂IPPD、具有受阻酚结构的亚胺氧化物化合物等,也有慌疲劳老化的作用,而用抗氧剂和抗臭氧剂并用的方法对疲劳老化的防护有更好的效果。